Адмиралтейские верфи — практически ровесник Петербурга. Пётр Алексеевич прекрасно понимал, что грозить шведу с берегов Невы можно, только опираясь на поддержку флота. И первое же серьёзное предприятие, появившееся в новом городе, конечно, занялось делом государственной важности — кораблестроением. "Адмиралтейский Дом" был заложен 5 ноября 1704 года. В будущем это предприятие стало ключевым и для отрасли, и для формирования границ Российской империи.
Три детали: здесь построили легендарный крейсер "Аврора"; рыбоперерабатывающая база "Восток" могла производить до 300 тыс. консервных банок в сутки; впервые в истории Каннского кинофестиваля призы за лучшую женскую и мужскую роли получил весь актёрский состав фильма о династии корабелов "Большая семья", который снимался именно здесь.
В нашем городе-музее трудно найти более историческое предприятие. Потому что таких, пожалуй, и нет — промышленный Петербург начался с Адмиралтейских верфей. Старинные здания, монументы, памятные таблички сконцентрированы здесь в такой плотности, какую можно встретить разве что в туристической локации. На территории предприятия — 14 объектов культурного наследия! При этом верфи остаются важнейшим судостроительным предприятием страны.
Коротко о главном
АО "Адмиралтейские верфи" — центр неатомного подводного кораблестроения России. Отсюда вышло почти 3 тыс. кораблей и судов различного назначения и класса. Здесь построено более 300 подводных лодок, в том числе 41 атомная, а 45 — на экспорт, 70 глубоководных и подводных аппаратов.
К началу Великой Отечественной отсюда выпустили треть всего боевого состава подводных сил ВМФ — 69 подлодок и 316 торпедных катеров. В 1959-м — атомный ледокол "Ленин", в 1969-м — глобальная рыбоперерабатывающая база "Восток", производившая до 300 тыс. банок консервов в сутки. В 2022-м — сдано заказчику научно-экспедиционное судно (НЭС) "Северный полюс" — уникальная ледостойкая самодвижущаяся платформа. В петровские же времена именно здесь заложили первый линейный корабль "Полтава", ознаменовавший новый этап в развитии русского флота. А ещё примерно тогда же тут построили и провели испытания первой в мире подводной лодки — "потаённого судна" крестьянина Ефима Никонова.
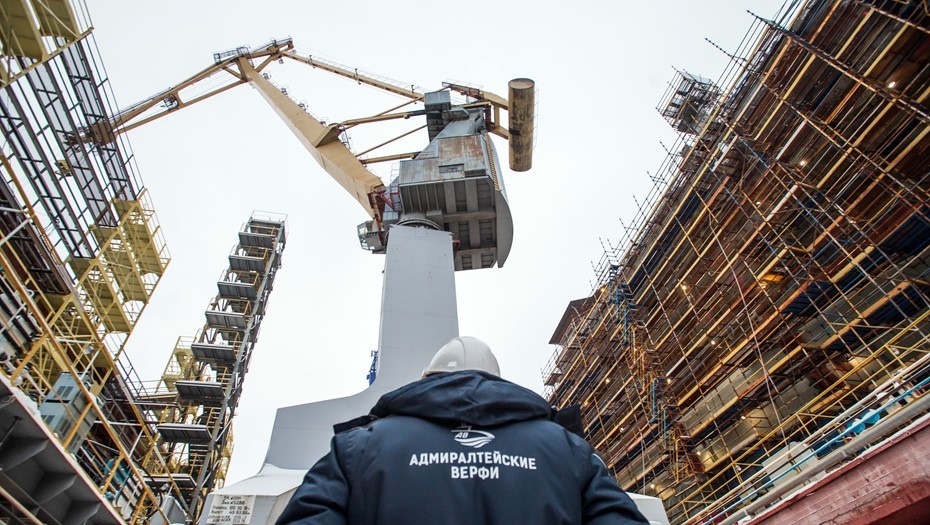
Сейчас в работе у предприятия — две серии подводных лодок для ВМФ России проектов 636 и 677. Также в постройке серия патрульных кораблей ледового класса для Военно-морского флота, серия больших морозильных рыболовных траулеров. В мае 2023 года завод заключил очередной контракт с Росгидрометом на строительство нового НЭС "Иван Фролов".
Вода и плазма
Первая точка экскурсии — цех металлообработки. Именно сюда приходит весь металл, который в дальнейшем станет деталями кораблей. Так что здесь, можно сказать, и начинаются будущие научные исследования северных широт, продовольственная общая безопасность.
В необъятных ваннах с водой лежат таких же космических масштабов стальные листы. Для примера: в абсолютных величинах одна из машин плазменной резки — 12 метров. Вот обрезок от детали — он весит больше 3 тонн. Целый лист, не обрезок, может достигать 9 тонн. На станок его помещают с помощью двух кранов.
Вода — необходимый элемент современных методов металлообработки. Сначала лист при помощи кранов укладывают на "постель", затем туда подают воду. Старший мастер участка объясняет, почему одни станки режут металл полностью в воде, другие — частично в воде, а совсем без воды — как в той песне. Никак. Ну, почти.
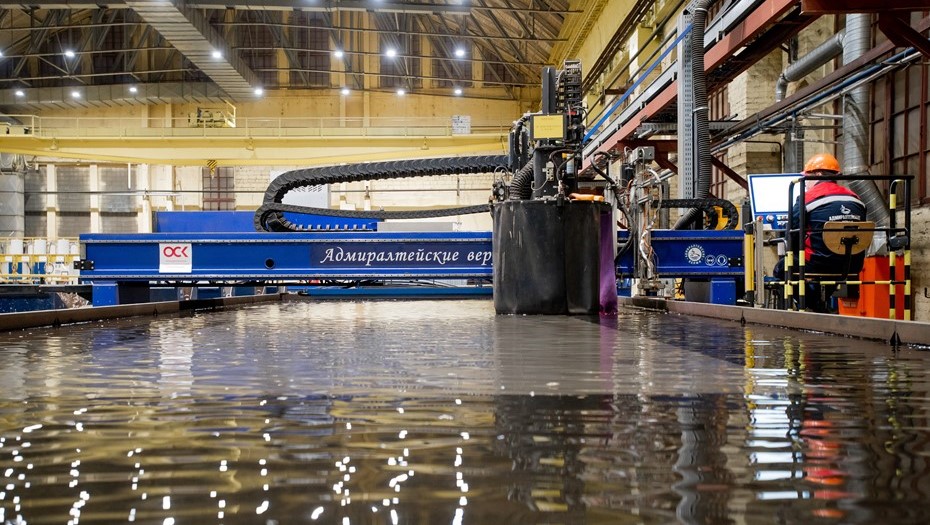
“
"Самые современные машины режут лист, который целиком помещён в воду — так деталь меньше деформируется. Есть станки постарше — там металл как бы лежит на воде, это нужно для сокращения выделения вредных газов. Ещё это зависит от толщины листа — толстый будут резать под водой, потоньше — на воде. А вот для работы с самым толстым металлом, от 35 мм, есть газовый станок, он режет на сухую. 120 мм — максимальная толщина листа на моей памяти", — рассказывает Максим Колмаков, старший мастер участка.
Такие детали нужны в машиностроении и в качестве подкладок под фундаменты. О них мы поговорим отдельно.
Оператор внимательно наблюдает за тем, чтобы плазменный резак точно следовал программе, и, если вдруг что-то пойдёт не так, должен оперативно отреагировать. Но мы экстренных действий не увидели, и это хорошо: значит, всё идёт по плану. Старинных станков мы тоже не увидели — здесь их нет, говорят, что технопарк постоянно обновляется. В планах на 2024 год — модернизация гибочного станка.
Процесс резки небыстрый. Укладка листа краном — раз. Подача воды — два. Позиционирование — три. Разметка контуров — четыре. И только после этого, собственно, резка. Итоговое время зависит от количества деталей и общей длины линий: чем больше — тем дольше.
После резки детали попадают на правильный станок — как ни стараешься избежать деформации, но полностью от неё не избавиться, поэтому перед окончательной комплектовкой детали проходят правку. А некоторые — гибку и снятие фаски.
На предприятии есть традиция — "торжественный рез". Это примерно как спуск на воду, но только в начале: так здесь отмечают старт нового проекта. В цеху собираются гости, после презентации заказа под музыку и аплодисменты начинается резка первого листа металла для будущего судна.
Сварщицы
Из мира плоскостей — к объёму. Следующий цех более наглядно показывает специфику предприятия — в этих фрагментах уже можно угадать будущие части судов. Мы на участке предварительной сборки. Здесь из деталей собираются укрупнённые узлы, которые отсюда отправляются на стапели. И потом из этих частей формируют судно.
Наш гид по слесарно-корпусному цеху, или, как он ещё называется, "участку №3 корпусного производства" — его начальник Владимир Клименко. На Адмиралтейских верфях работает с 1980 года. Заслуженный машиностроитель России, почётный судостроитель России. А 3 ноября 2023 года он получил медаль к ордену за заслуги перед Отечеством II степени.
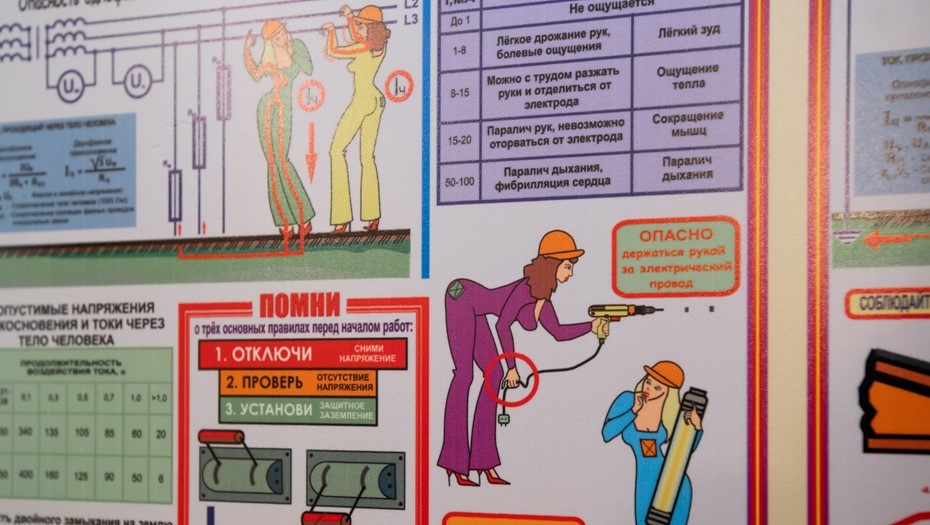
Владимир Николаевич рассказывает удивительную историю — долгое время в его цеху работали сварщицы. Их отличали аккуратность, внимание к деталям и к собственному внешнему виду (на этих словах руководитель с сожалением вздыхает — "ушли дамы"). Работа физически очень тяжёлая.
“
"Сварщик же не только сидит и варит что-то. Это надо перетащить с собой сварочный аппарат. Одна только кассета сварочной проволоки весит 5 кг. Всё остальное оборудование — ещё килограммов десять. И так 15 кг под мышку — хвать! — и пошла. А за ней ещё тянется шлейф питания. Плюс газовая горелка!"
Фундаментальное
Владимир Клименко знает толк в визуальных эффектах. Нам наглядно демонстрируют разницу в зачистке двух видов металла — обычной углеродистой стали и титанового сплава. Когда начинают обрабатывать первую, от поверхности отделяется сноп красивых жёлтых искорок. Второй же создаёт новогоднее настроение — белые звёздочки больше всего похожи на бенгальские огни. Потому что в состав сплава тоже входит магний. Смотреть можно бесконечно — красиво. Это, конечно, лирика, но операция нужная: детали покрыты грунтом, не зачистишь его — сварной шов будет с дефектами. А что феерично, так это бонус.
Большая часть помещения занята странными конструкциями самых разных форм и размеров. Кажется, что нет ни одной одинаковой, как у снежинок. Одна из них похожа на крестовину для ёлки, другая — на небольшой дом. Аналогии для других подобрать сложно. Это — фундаменты, о которых мы писали выше. Необходимые детали для крепления различных узлов. Та, что похожа на дом, будет держать двигатель. Но, оказывается, не всё то, что ни на что не похоже, — фундамент. Один из них оказался цистерной для топлива.
Элементарно, Ватсон!
Некоторые вещи настолько очевидны, что кажется странным, как это их ещё нет в остальных местах. Вот, например, передвижная скамейка для различных работ — пока её не придумал Владимир Николаевич, приходилось ходить пешком, перенося на себе тяжёлый сварочный аппарат. Собирают скамейки из подручных материалов, поэтому все они почти так же индивидуальны, как фундаменты. За это улучшение Владимира Клименко отметило руководство завода.
Или вот — органайзер для кабелей. Казалось бы, просто Т-образные кронштейны, которые позволяют протянуть провода от передвижного оборудования поверху. А сколько пользы! Ведь раньше все эти бесчисленные кабели лежали на полу, мешая передвигаться. Тоже решение местных сотрудников.
“
"Элементарная вещь: воздушный шланг, которым работают пневмоинструменты. В других местах сотрудник закончил работу, свернул шланг и понёс к себе в шкаф. У нас они хранятся просто на кронштейне, они общего пользования. Он висит в том месте, где могут вестись эти работы. Ну зачем на себе тащить куда-то то, что там и так может лежать? Пусть будет два комплекта, в итоге всё равно будет выгоднее".
Плавучий завод
И вот, наконец, они. То, ради чего работает весь завод: два исполина, которые в конце 2025 года отправятся бороздить просторы Берингова и Охотского морей, а также прилегающие к ним районы Восточного побережья России. Это новейшие морозильные рыболовные траулеры, одни из самых современных в мире рыбопромысловых судов.
“
"Таких больших и мощных в России ещё не было. Даже заказчик их называет "супертраулер", потому что объём перерабатываемой рыбы очень большой. Предназначены они для переработки минтая и сельди, причём для полной безотходной переработки. Там находится и рыбоперерабатывающая фабрика, и рыбомучная установка. Производственная мощность — около 80 тыс. тонн рыбы в год", — поясняет Сергей Брусницын, заместитель главного строителя.
Таким образом, весь улов превращается в полезный продукт: замороженное и уже упакованное филе, фарш, сурими, икру, молоки, а также рыбий жир и рыбную муку. Производительность морозильной установки — 250 тонн в сутки.
Траулеры оснащены инновационными энергетическими установками с "плавающей" частотой электросети. Эта технология позволяет валогенератору при тралении работать на сниженных оборотах главного двигателя, что значительно экономит топливо.
Траулеры имеют повышенный ледовый класс, благодаря чему могут работать в отдалённых от берега районах, в том числе в Арктике и Антарктике. Поиск рыбы и контроль траловых операций проводится с помощью гидроакустических приборов. Это один из самых серьёзных "гражданских" проектов завода.
Первые три траулера серии уже ставят рекорды производительности на Дальнем Востоке. Следующее судно, "Капитан Мартынов", будет сдано в конце января. Ещё два — "Капитан Щербаков" и "Механик Юнаков" — пока на стапелях, их достроят к концу 2025 года. Завершить серию из 10 траулеров планируется в 2027 году.
Рождение судна
К слову, о стапелях: они тоже необычные — наклонные. В советское время такие были только на трёх заводах. Причём два из них — ленинградские. Ещё здесь находится один из самых больших в России стапелей — длина его 274 метра, ширина — 34. Зимой до конца его пройти сложно, если ты не одет как местные работники. Холодно.
Александр Чапов, заместитель начальника стапельного цеха, рассказывает, что наклонный стапель, с одной стороны, создаёт определённые сложности при постройке, поскольку приходится учитывать углы и нагрузку, но с другой — в финале судно спускается на воду под собственным весом, и это величественное зрелище заставляет забыть обо всех трудностях.
С одного из этих стапелей в своё время спустили на воду первый в мире атомный ледокол "Ленин". Тут даже установлена памятная табличка в честь этого события, а на одном из стендов есть модель спуска. Серия 2010 года — два уникальных танкера, "Михаил Ульянов" и "Кирилл Лавров": усиленный ледовый класс, дедвейт 70 тыс. тонн, длина — практически весь стапель, 254 метра. Во время спуска такой танкер под собственным весом почти доходит до Балтийского завода — это на другой стороне Невы.
Последние 6 часов перед окончательной точкой постройки судно связывает с заводом (и со стапелем) одна-единственная металлическая балка. Прочная, конечно, но относительно размеров судна её почти не видно. А потом её обрезают — и всё, заказ готов.
У каждого корабля есть крёстная мать. Её объявляют при спуске судна на воду. Именно крёстная мать разбивает о борт бутылку шампанского. А потом следит за судьбой своего крестника.
О людях
В начале декабря 2023 года Адмиралтейские верфи заняли первое место в конкурсе на лучшую корпоративную программу "Здоровая рабочая среда". На предприятии созданы все условия для комфортного и безопасного труда, есть возможность для занятий физкультурой и спортом, получения квалифицированной медицинской помощи. Завод разработал систему обучения работников, чтобы уровень знаний сотрудников соответствовал статусу предприятия. На Адмиралтейских верфях активно применяется институт наставничества. Задача наставников — не только научить, передать опыт, но и способствовать комфортной адаптации молодого специалиста в компании, его профессиональному росту.
Для многих это больше, чем просто средство заработка: здесь работают из поколения в поколение. Общий стаж некоторых династий — более 100 лет.
Сейчас уже невозможно представить, каким был бы город без Адмиралтейских верфей. Как минимум у него был бы другой ландшафт — строительство завода меняло русла рек и каналов. Но это частности. А глобально — без всех тех кораблей, что отсюда вышли, история России могла пойти совсем другим путём. Предприятие сохраняет своё значение для страны и по сей день, оставаясь не только важнейшим судостроительным комплексом, но и одним из крупнейших налогоплательщиков и заказчиков наукоёмкой продукции.